Lean Manufacturing na Logística de Armazéns
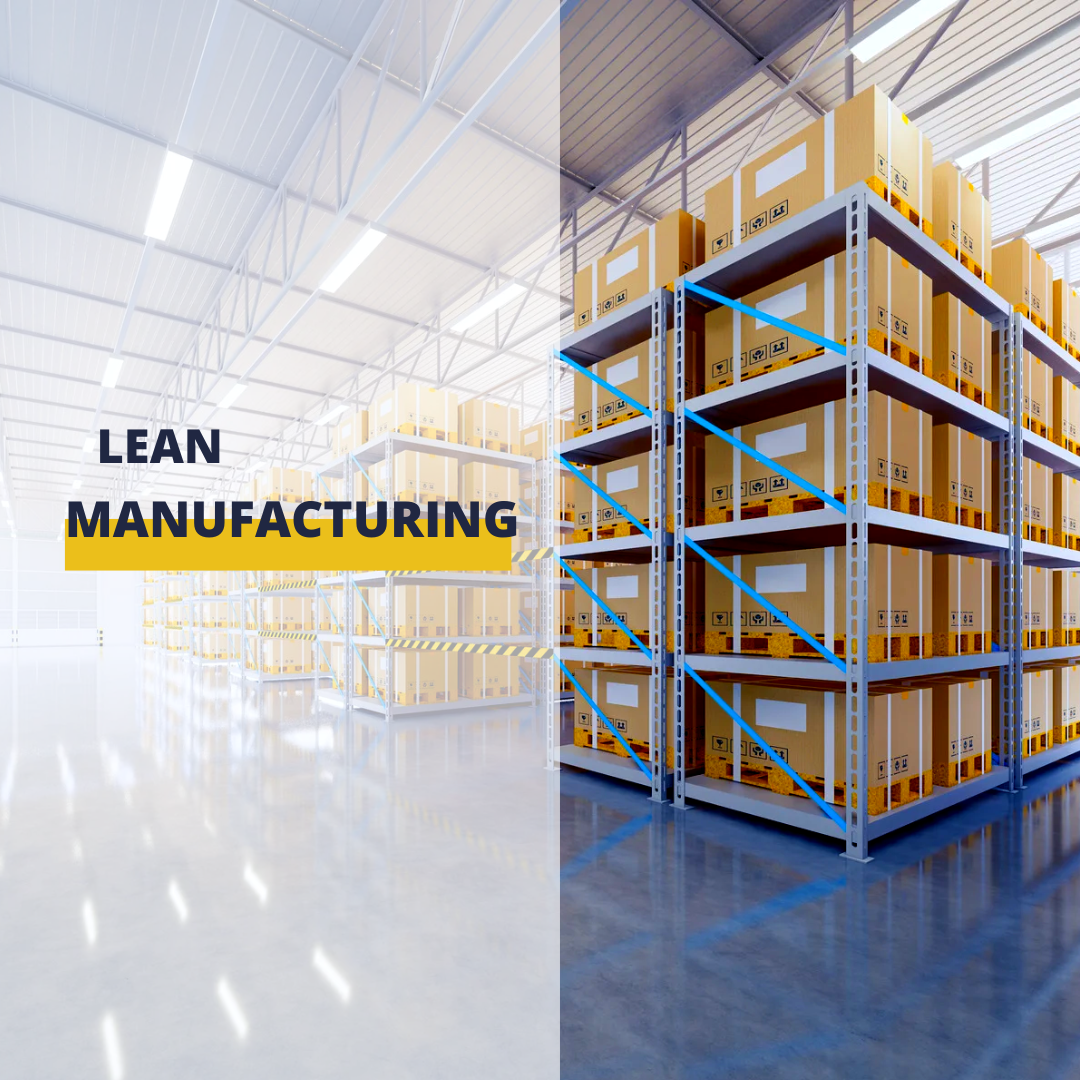
Lean Manufacturing na Logística de Armazéns
Conheça os 5 desperdícios Lean
O Sistema Toyota de Produção e Lean Manufacturing
O objetivo deste artigo é apresentar as ferramentas básicas do Lean Manufacturing e sua aplicação na área de outbound de um centro logístico de distribuição.
O sistema TOYOTA de produção é muito discutido, porém a aplicação dos conceitos criados por Kichiro Toyoda na década de 1950 ainda é complicada, pois exige muita disciplina e mudança de hábitos e conceitos dentro da empresa.
Neste artigo iremos abordar os 5 tipos de desperdícios que o Sistema Lean Manufacturing visa eliminar.
Os 5 desperdícios que o sistema Lean Manufacturing visa eliminar são:
1. Superprodução
2. Tempo de espera
3. Transporte e movimentações de materiais
4. Processamento e defeitos
5. Estoque
1 A superprodução
A superprodução é o maior desperdício dentro da
operação por gerar um tipo de estoque demasiadamente perigoso: o estoque em processo. Este é o único tipo de estoque que a empresa não consegue vender pelo preço adequado.
2 Tempo de espera
Foram identificados diversos pontos onde o tempo
de espera pode ser eliminado ou reduzido em quase
sua totalidade. Somente após o término da separação
dos pedidos das gaiolas feitos nas bancadas, as caixas
de papelão para embalagem eram coletadas e depois
enviadas à esteira para etiquetagem. Os tempos maiores
de pedidos para esteira de etiquetagem, e da esteira de
etiquetagem para a paletização.
3 Transporte e movimentações de materiais
No transporte de materiais foram identificadas possíveis melhorias no material rodante. O picking de materiais por diversas vezes era feito por meio de empilhadeiras e posteriormente transferidos para as gaiolas antes de serem enviados para a áreas de embalagens.
Outros materiais eram coletados diretamente nas gaiolas e enviadas para área de embalagem. A movimentação das embalagens dentro da área era feita de forma desordenada.
4 Processamento e defeitos
Após a chegada das gaiolas na área de embalagem, uma pessoa separava os pedidos de diversos clientes, que chegavam misturados nas gaiolas, para envio à esteira de embalagem. Muitas vezes faltavam e sobravam itens e a gaiola era devolvida ao picking.
5 Estoque
Para garantia da produtividade da área de embalagem, era necessário um estoque em processo antes da separação dos itens dentro das gaiolas. Tal procedimento aumentava a área necessária para operação gerando custos.
Conclusão
Através desse artigo pudemos observar claramente a importância do uso de ferramentas adequadas alinhadas ao planejamento.
Desta maneira, o Lean Manufacturing proporciona um aumenta em grande escala no fluxo de materiais dentro da operação através da redução de desperdícios e retrabalhos de tal forma a se obter uma maior satisfação de todos acionistas e interessados na operação sem a perda do foco e do valor na visão do cliente.
Não Perca Nenhuma Atualização!
Você sabia que publicamos novos conteúdos a cada 15 dias?
Mantenha-se atualizado com dicas que vão transformar sua carreira.
Autor
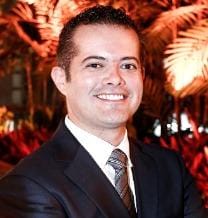
Paulo Roberto dos Santos Tavares
Fundador do Instituto TCT
Executivo com mais de 20 anos de experiência em Supply Chain Management e ocupou cargos importantes em diversas empresas, dentre elas Thyssenkrupp, Natura e Bosch. Professor nos cursos de MBA da FGV, USP e Albert Einstein. Autor de 4 livros e dezenas de artigos na área. Consultor internacional em Supply Chain e atua em mais de 15 países em projetos de ponta a ponta na cadeia de suprimentos. Mestre em Engenharia de Produção e Manufatura, estudou sobre Blockchain na Cadeia de Suprimentos. É pós-graduado MBA em Gestão Logística pela FGV, especializado em empreendedorismo pelo Babson College em Boston EUA e graduado em Administração de Empresas. Especialista em Gestão Ágil e Inovação pela FGV.